Die Lubricants
Our die lubricants are engineered to actually enhance your processes, allowing you to gain efficiency. Die lubricants can be engineered to provide exceptional release and die/solder protection with optimized wetting, promote metal flow, quickly cool die surfaces, and maintain a die temperature within a narrow band, all of which allow for faster cycle times and longer die life.
VIDEOS
How Does Chem-Trend Support the Die Cast Industry?
Global Sales Director, John Belyk, explains how Chem-Trend anticipates and adapts to the needs of the die cast industry, with a focus on electric vehicle (EV) production.
Die Casting: Inside Chem-Trend’s 360-Degree Die Lubricant Testing & Validation Process
Gain an insiders look at Chem-Trend’s high performance die lubricant testing and validation process done in collaboration with the molding and joining experts at TU Braunschweig and surface treatment specialists at sister company, SurTec.
NEWS
RELATED THINKING
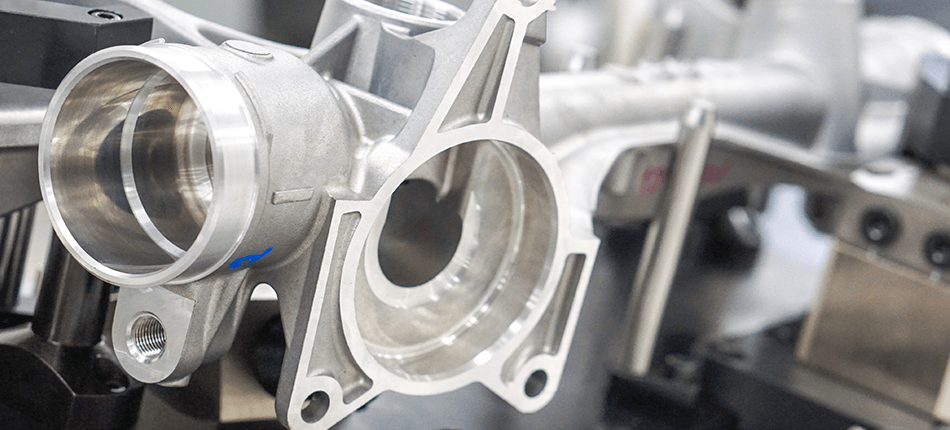
The Effect of Die Lubricant Spray on the Thermal Balance of Dies
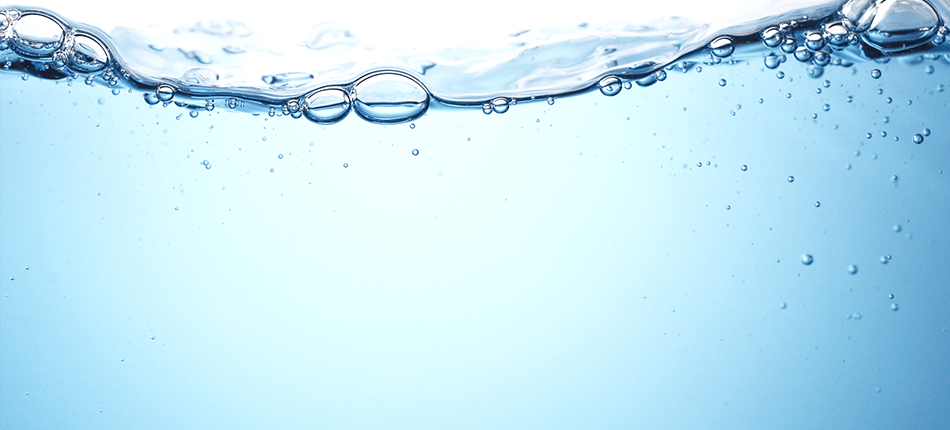
Water Conservation through the Utilization of Advanced Performance Die Lubricants
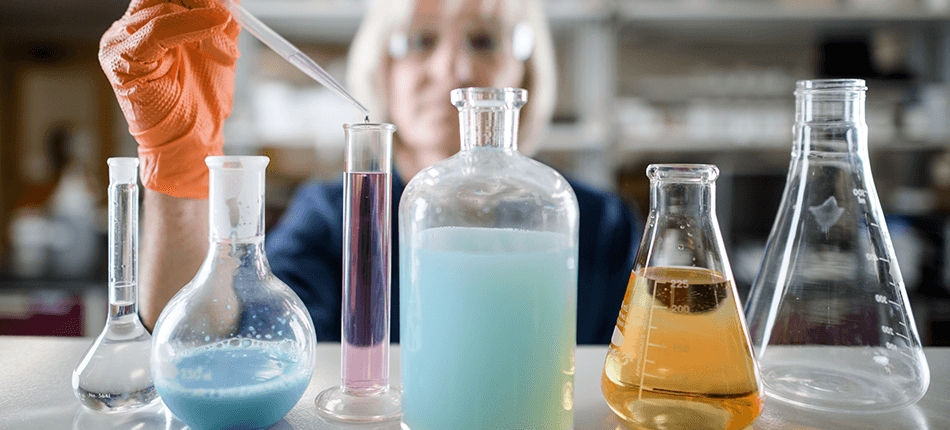
Innovative Die Lubricant Trends for Evolving Productivity and Process Requirements
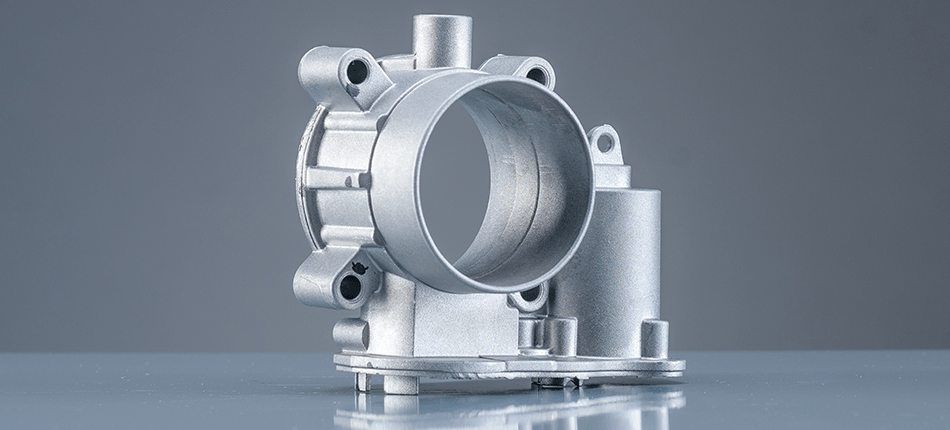
Magnesium Die Casting Lubrication Technology & Trends
BROCHURES
Automotive E-Mobility: Driving Manufacturing Forward
Chem-Trend empowers the world’s leading OEMs and automotive suppliers by enhancing the efficiency and ease of industrial molding applications.
Chem-Trend® SL-60XXX
The high-quality products of the Chem-Trend® SL-60XXX series help manufacturers produce easy-to-clean casting parts that are also suitable for use in heat treatment applications. The release agents in the series are cathodic dip coating compatible (CDC-compatible) so they do not affect metal coatability, even with CDC processing. Post-processing by means of seal or structural bonding presents no problem – the release agents allow optimal bonding to other materials as well.
HERA™ Die Lubricants
Chem-Trend’s HERA™ — High Efficiency Release Agent — die lubricant helps manufacturers reduce scrap, downtime and energy use. Its water-based formulation can be used in a variety of applications, and its performance characteristics make it an ideal solution for both high and low temperature operations.
HERA™ Light
An even application of release agent to the mold is required to obtain a consistent high-quality surface finish. Irregularities lead to defective mould parts and hence to scrap. Incorrect spraying further reduces tool lifetime. To prevent all this, Chem-Trend has developed an innovative UV responsive formulation for the HERA™ product series that helps ensure results through appropriate application.
Delivering customized solutions for the toughest die casting challenges
Chem-Trend die lubricants have been the industry standard of performance for almost fifty years. Download our brochure to find out more about a long history in the Die Casting industry.
FAQ
Gas porosity can occur when the turbulence of the molten metal traps gas inside the casting. Excess die lubricant can create more gases in the cavity that may contribute to gas porosity. High efficiency die lubricants do not contribute significantly to gas porosity.
The main source of smoke is usually the plunger lubricant. These are usually organic compounds and there is a tendency to overfeed these products. High efficiency and low smoke plunger lubricants can minimize the smoke in a foundry. Die lubricants are usually water-based products and therefore are not major contributors of smoke. Some oil-based die lubricants can produce smoke but are typically fed at very low dosages and so the quantum of smoke produced is not significant.
The paintability of a casting is more dependent on the efficiency of the cleaning process. Silicone containing die lubricants can be used to make paintable parts, but they must be easily cleanable by most cleaning processes. Because of the wide variation in the types of cleaning process and the cleaners used, we advise customers to check the efficiency of cleaning before finalizing the product.
COD stands for Chemical Oxygen Demand and all organic compounds create COD. In the case of die lubricants, typically a significant amount of the organic materials can be removed by precipitation or filtration as described above.
Die lubricants that are designed to rapidly cool and adhere to the die surface form a protective film that prevents solder and provides lubricious release of the casting. This can reduce both the cycle time and down time, improving productivity.
The dilution ratio of die lubricants can be checked by using a LaMotte meter. A sample of the dilute die lubricants is placed in the instrument and the reading is compared against a standard calibration curve. Automated systems for checking the dilution automatically are also available.
Water based die lubricants are typically emulsions of oils and other actives in water. The size of the emulsified particles is an important issue. Small particles can be removed in conventional precipitation style waste water systems using alum and lime or similar reagents. They can also be removed by semi-permeable membranes like UF and NF although these may have a tendency to foul (depending on the type of membranes used). The removal efficiency depends on the type of process used.
While die cooling is an intrinsic property of many die lubricants, it is not the most important property. For some applications a lot of cooling may be undesirable as it can adversely affect the filling of the cavity with molten metal. Other applications may involve dies with little or poor internal cooling. For these applications a die lubricants that can cool very efficiently would be desirable.
There is no one optimal ratio; this has to be established for every machine and application. The ideal dilution ratio is one that provides the right amount of lubricant film in the shortest spray time possible.
We suggest using soft water for diluting water-based die lubricants. Water with up to 100 ppm of total hardness has been used with no adverse effects. Very pure water (less than 10 ppm hardness) can lead to corrosion problems on the die, while high hardness water can lead to other problems like spray nozzle plugging and in cavity build-up. Using good quality water can reduce downtime and give better quality castings.
Typically plants use either a centralized system (which serve a number of machines), or individual dilution tanks which are dedicated to one die cast machine. Centralized systems simplify the task of making dilutions and can save cost of equipment. The disadvantage is that if different die cast machines have different operating conditions, it will be difficult to change the dilution ratio or the die lube. Individual dilution tanks allow very tight control of dilution and are preferred when part quality is of very high importance.