Smoother waters for a powerboat manufacturer.
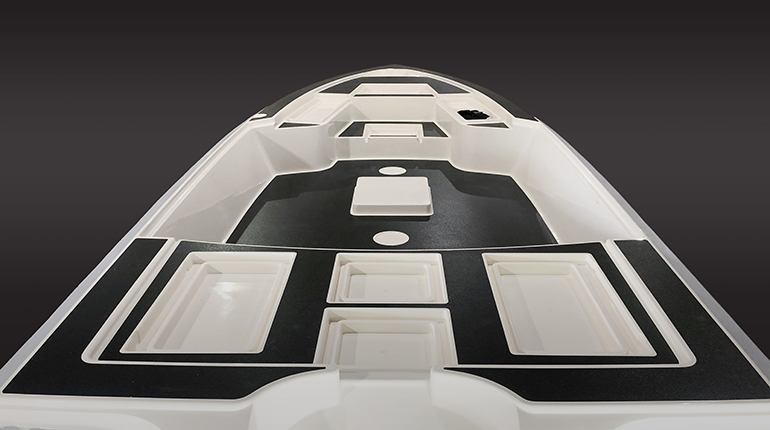
WHAT WE ACHIEVED.
A leader in the recreational boating industry was experiencing rampant prerelease problems when making molds for boat hulls, decks, and small parts from plugs, costing them significant man hours for post-finish rework for every single mold. Chem-Trend was able to identify a sealer-and-release- agent combination that not only solved the problem, but also challenged the accepted norm of paste wax. By introducing a unique hybrid release solution that combined the best of paste wax with a true liquid semi-permanent, the manufacturer achieved highly favorable results that led to operation-wide implementation.
HOW WE GOT THERE.
Chem-Trend was truly an extension of the customer’s team throughout the process. We were able to visit the customer’s facility and experience the entire mold manufacturing process. This enabled us to quickly identify problem areas as well as areas of opportunity to improve production efficiency.
We were concerned with two extremes visible in the process:
1) Product sticking to the mold due to excessive surface roughness
2) Prerelease due to lack of process control
Our global research and development teams collaborated with our local sales and technical service team members to outline the best approach and iteratively test over 40 different product combinations in our labs, which allowed for a refined selection of only the most viable options to be tested on-site at the customer. This approach limited the customer’s need to interrupt the production process as well as any undue stress as a result of in-house testing. Together, we were able to find a solution that offered consistently superior results without the need for rework.
OUR SOLUTION.
We combined Chemlease® Sealer 2697 with Chemlease® 2185 to produce the ideal solution. The use of a semi-permanent release agent in place of exclusive use of the industry-standard wax positively impacted the production process.
Typical environmental factors became less of an issue for the customer’s application after implementation as well. For example, application of paste wax is a very laborious activity, requiring considerable time and effort to polish to a Class A finish. And when applying in warm weather environments, this effort can result in operator fatigue.
The new system was presented as a trial to the manufacturer and showed no signs of sticking or prerelease issues. The trial quickly moved from testing on a small box console to a 65-foot deck plug, and the results were clear. The prerelease on the plugs had been virtually eliminated, opening up the product testing to all production facilities.
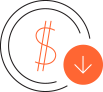
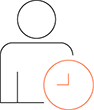

DATA INSIGHTS
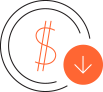
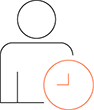

HANDPRINT IMPACT
At Chem-Trend, we pride ourselves on our long history of sustainability efforts. However, it is our effect on our customers’ processes that provides the greatest impact. It goes beyond our global Footprint; it is our even wider Handprint.
Here, we achieved the following:
- Leaner processes, leading to reduced energy needs
- Less product used
Materials
Energy